PERSEUS, which stands for “Promoting Excellence & Recognition Seal of European Aerospace UniversitieS”, successfully held its Kick-off Meeting on December 9th 2014 at the Department of Aerospace Science and Technology, Politecnico di Milano, Italy. The PERSEUS Coordination and Support Action, funded by the EC’s Horizon2020 Research & Innovation Programme, aims at firstly defining the evolving skill needs of the European aviation sector and subsequently at formulating strategic
recommendations and corrective measures for the improvement and harmonization of the content of the curricula for aviation engineers towards the ultimate creation of an integrated European aviation education system, based on sound quality criteria capable of supporting the continuous improvement of the educational system in the sector.
For more information please visit the PERSEUS project website.
SUNJET II (SUstainable Network for Japan-Europe aerospace research and Technology cooperation II) initiated its activities with a very successful Europe-Japan Symposium on "Electrical Technologies for the Aviation of the Future". The two day symposium was held on 26-27 March 2015 in Tokyo and was hosted by the Delegation of the European Union to Japan. The symposium focused on the current status of the European and Japanese future trends of the electrical technologies for the aviation and gathered around 180 participants. A number of excellent presentations, which will soon be available on the SUNJET II website, were given from the most important European and Japanese stakeholders.
SUNJET II is a support action funded by the European Commission, aiming at enhancing the relations between EU and Japan in research and technology activities related to aviation. SUNJET II is expected to open new application domains for future aeronautics EU-Japan cooperation agreements, aiming at EU-Japan compatibility, better interfacing and paving the road for common regulations, rules and procedures as well as the use of interfaced or common subsystems, equipment and tools.
More information will soon be available at the SUNJET II website.
With 1,5 years of operations under its belt, the CATER Coordination and Support Action has reached several achievements. A dedicated Door-to-Door (D2D) model in daily journey has been established, thereby creating a common language and understanding for the theme of time efficiency. Moreover, through a very comprehensive analysis, the most relevant Research and Innovation domains connected to time efficiency have been found and have accordingly defined an R&I framework.
The developed Assessment Framework has been utilized to assess past and running (FP6 &FP7) EU-funded projects (63 so far), and leveraged to identify future evolutionary needs and opportunities.
Furthermore, an online expert consultation survey on R&I issues in Time efficiency has been launched, aiming to accumulate the viewpoint, expertise and valuable insight of the main R&I players and aviation stakeholders. If you wish to participate in our consultation campaign, please fill-in the CATER questionnaire here.
The process is very simple and should not take you more than 10 minutes to complete. Additionally, the CASK web-platform –a smart and innovative instrument to search for everything related to the world of travel efficiency- has been released and made accessible to the wide audience, to turn it into a proactive CATER Community.
You can register and become part of the CATER R&I Community here. Also, you can join our LinkedIn Group here.
Finally, the 2nd CATER e-book is now available online.
Approaching its final stage, the Promo – Air project is organizing its final Workshop that will take place on April 23rd 2015, in Brussels, Belgium. The objectives of this event are to inform the aeronautical stakeholders about the achievements of the Promo-Air initiative, present the lessons learned from the process of getting in contact with European high-school students and identify a roadmap towards additional actions and policies required for further stimulating young Europeans towards this aim.
The aforementioned action is combined with the organization of the European Aeronautics Science Week. In this event, high-school students from all over Europe have the opportunity to visit Universities of their local societies and explore the fascinating world of Aeronautics through the produced by Promo-Air educational material. This initiative is expected to contribute to the raising of awareness of young Europeans in studies related to Aeronautics and in the same time to link European high schools with Universities dealing with aeronautical research. In parallel, a pan-European student quiz competition has been settled, the winner of which will be offered an all-paid visit to Airbus Assembly Line, in France generously sponsored by Airbus S.A.S. and EASN Association as well.
For more information on the Promo-Air project, please visit the promo-air website.
Having completed its project duration, HIKARI held its final meeting from the 14th to the 15th of January 2014 in Suresnes, France. During this two day meeting, the very positive outputs achieved were presented and received enthusiastically by participants. This final meeting closed a successful period of project activities, yielding constructive feedback, which concluded that there is still room for further research on the crucial field of High Speed Transport (HST).
In the same time, the inclusion of a TV documentary in the Euronews channel has been produced, with regards to the research performed within HIKARI. The aim was to create a video, with which HST will gain awareness in in our daily life, allowing us to conceive it as a feasible scenario for our future by giving us the opportunity for example to fly from Paris to Tokyo in less than three hours! This TV documentary was aired in the FUTURIS programme in 13 different languages and reached 400 million households in 155 countries.
For viewing the TV Clip and the respective article please follow this link.
For more information visit the HIKARI project website.
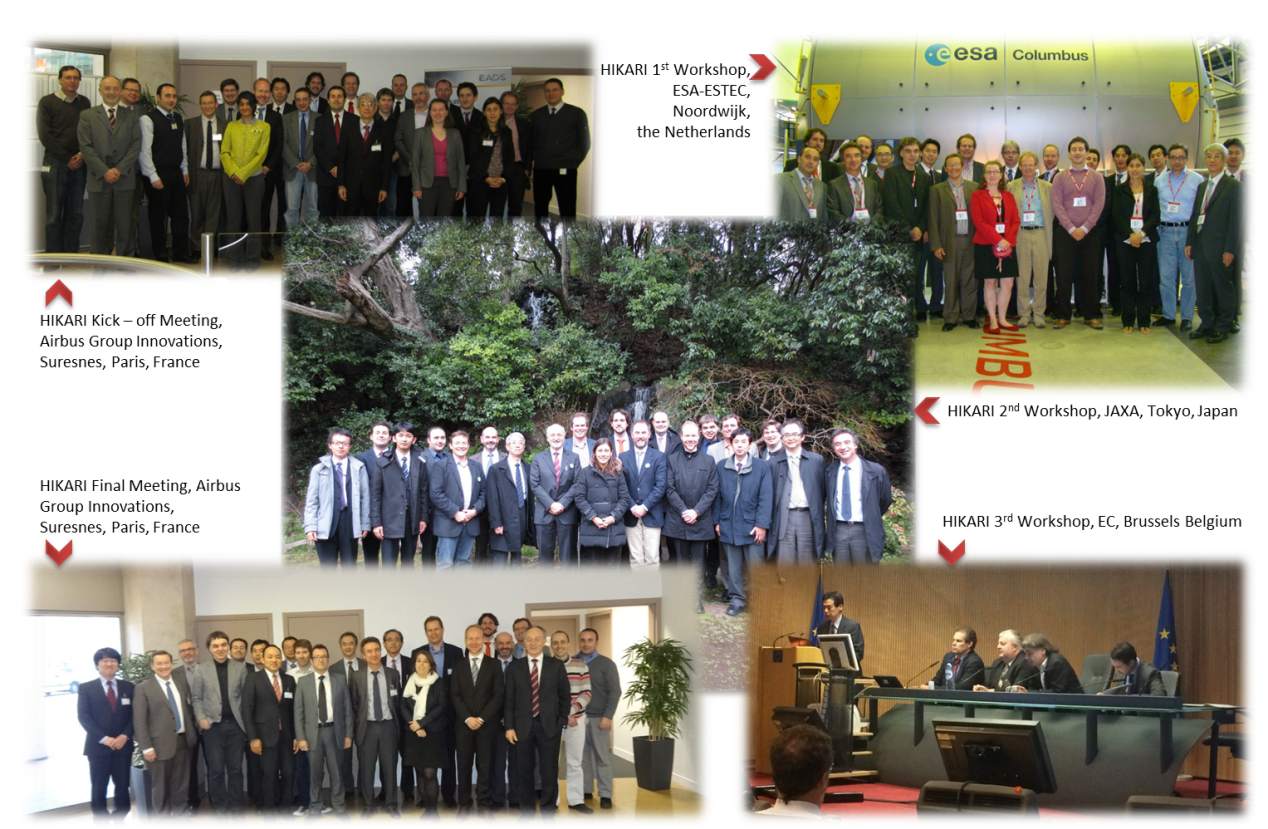
The UMRIDA project aims at the improvement of Uncertainty Quantification (UQ) methods towards industrial readiness, focused on handling a large number of uncertainties (including geometrical ones), epistemic uncertainties, analysis of input uncertainties and methods for defining tolerances. The proposed methods are being validated and evaluated against selected test cases, towards the development of the UMRIDA Innovative database for UQ and Robust Design Management (RDM). Preliminary UQ results have been achieved for the Rotor 37 and the RAE2822 airfoil challenges, by taking into account a large number of
geometric and operational uncertainties. The results obtained will be presented in the upcoming 1rst UMRIDA Workshop on Uncertainty Quantification. In the second half of the project, robust design formulations will be developed and applied to other test cases, aiming to achieve results in reasonable time, by combining efficient UQ methods and existing optimization methods.
For more information please visit the UMRIDA project website.
SARISTU has completed the first half of its final year and is on the road to its Final Conference and Meeting to be held in May 2015 in Moscow, Russia. Some of the key highlights of this period include the delivery of the completed 5X4m Door Surround Structure with 584 co-bonded sensors from Invent to DLR’s Stade facility. Furthermore, the static test of the Enhanced Adaptive Droop Nose Ground Test Demonstrator successfully took place at VZLU.
To top it all, the SARISTU Wind Tunnel Demonstrator was fully assembled, with system installation completed and performed its first flight on board a cargo aircraft to Moscow for Wind Tunnel Testing. In a nutshell, the overall progress is meeting and in individual cases exceeding expectations through additional test campaigns regarding Nanocomposites and the initial assessment of multi-SHM equipped test specimen. This is also highlighted by the increased visibility and awareness of the project.
For more information please visit the SARISTU project website.
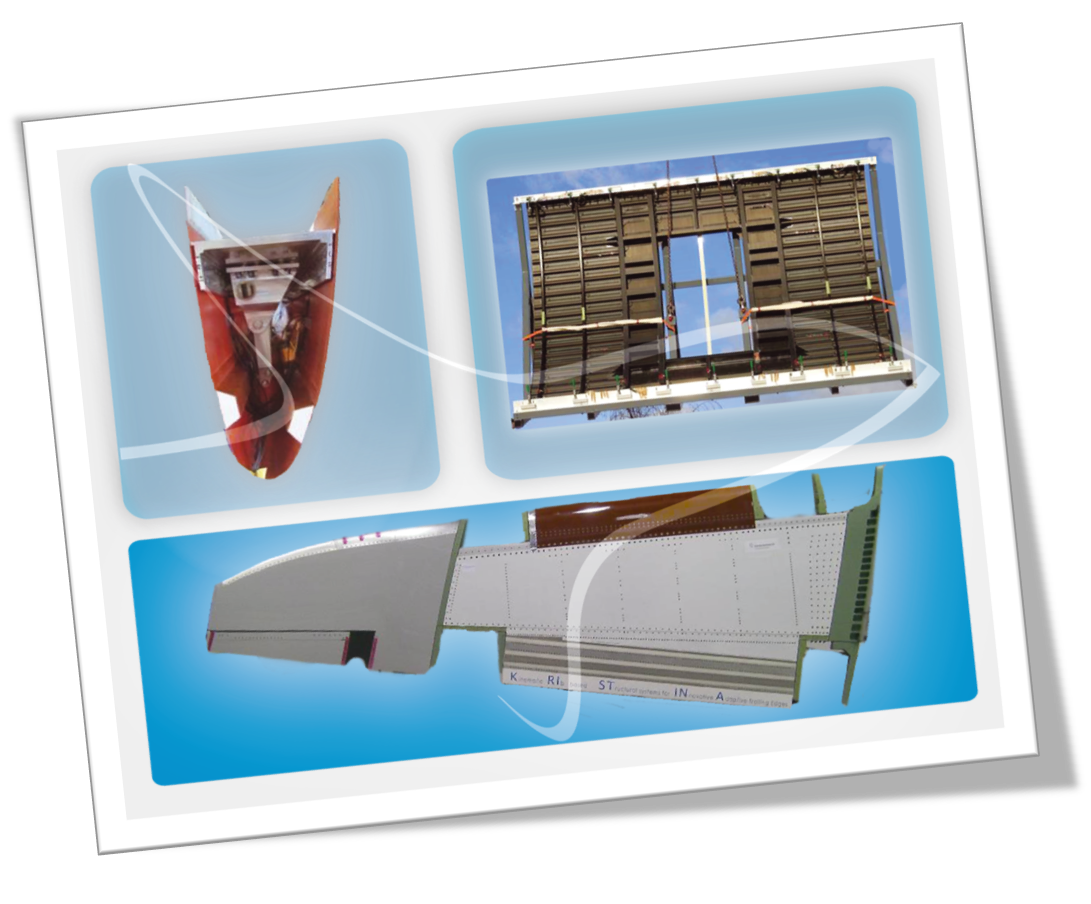